Type 5 Building Construction Explained: Materials, Risks, and Homeowner Tips
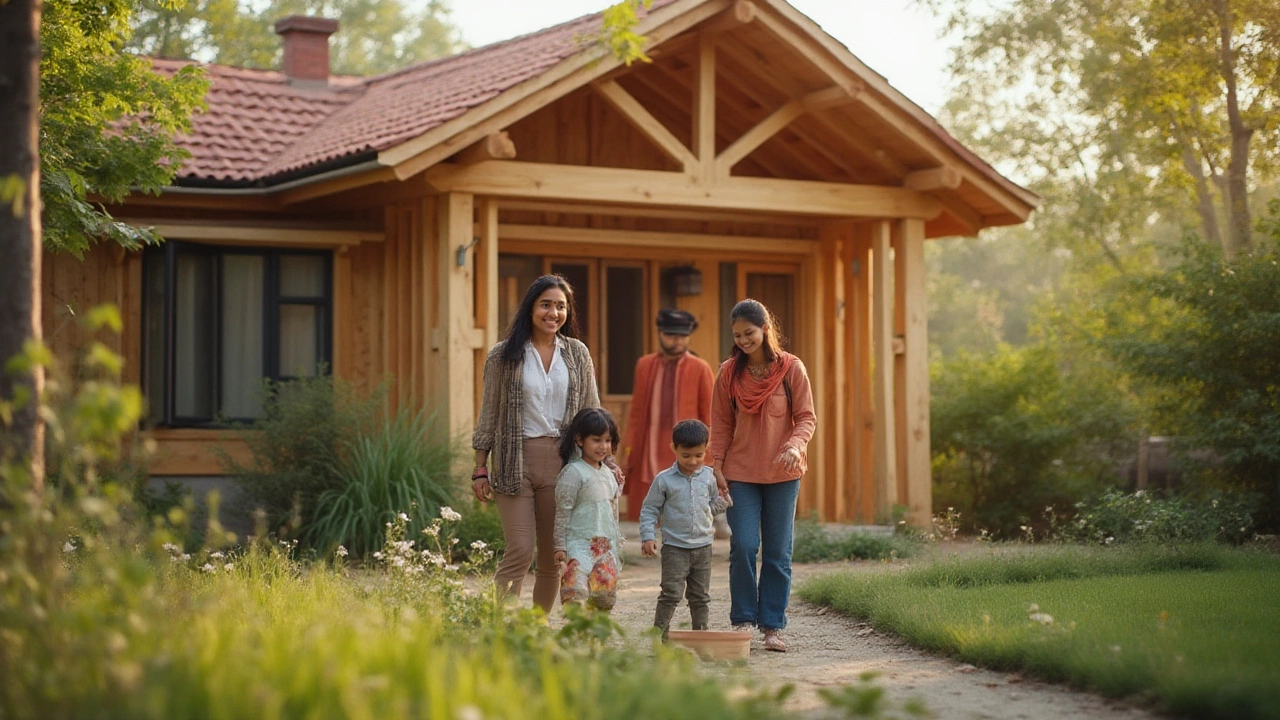
Picture your neighborhood: houses lined up, maybe some townhomes thrown in, a row of charming bungalows. You probably don’t think much about what’s holding all of it together, right? But here’s the thing—most of these homes, especially the single-family types and smaller apartment buildings, are built under something called Type 5 construction. It’s everywhere, yet folks rarely dig into what it really means for the places where we live and raise our families. If you’ve ever stared at a freshly-framed house or wondered why wood seems to rule the suburbs while sturdy brick is all downtown, you’re about to find out why.
What Is Type 5 Building Construction?
Type 5 construction is the go-to for residential buildings in the United States, and it’s almost always about wood. Imagine the skeleton of your house—studs, floor joists, roof trusses—all made from lumber. That’s the core of Type 5. The International Building Code (IBC) officially classifies this as "wood-frame" construction. You might stumble across old-school terms like "stick-built" or "platform framing"—they’re talking about the same thing.
This method isn’t new. People have been building with wood for centuries, but today’s Type 5 homes aren’t quite like little log cabins from the past. Now, dimensional lumber, wooden trusses, and engineered products—think plywood, OSB (oriented strand board), even laminated veneer lumber—are all common. The versatility of wood leads engineers to push the limits: homes, three-story apartments, townhouses, and condos all pop up using this style. Think of any traditional homey neighborhood, and you’ll probably spot dozens of Type 5 buildings.
What makes Type 5 stand out is that even the exterior walls can be wood. That’s different from Type 3 or Type 4 buildings, which rely on brick, block, or heavy timber for those critical outside walls. It’s lighter, easier to put together, and cheaper to truck around—one reason American suburbs stretched so far, so fast, after World War II.
Back in the late 1950s, the suburban boom hit hard. The cost was king, and Type 5 answered the call. Builders realized that two-by-four framing and mass-produced trusses made construction way faster. By 1970, more than 60% of U.S. homes were wood-framed—the vast majority Type 5. Speed, flexibility, and affordability combined to dominate how North Americans built homes.
So why do codes label different "types" of construction at all? Safety. Each type indicates how well a building copes with fire and structural loads. Type 1 (like concrete and steel skyscrapers) offers the most burn time and strength. Type 5, on the other hand, offers the least fire resistance—because wood, after all, burns. That trade-off sits at the heart of its risks and rewards, especially for homeowners and designers.
Materials and Methods: Inside the Wood-Frame World
It’s wild how much can be done with simple lumber. Your typical Type 5 building is a puzzle of interlocking parts: wood studs every 16 or 24 inches; top and bottom plates; joists stretched out for second stories or attics, fastened with metal hangers. The techniques sound simple, but they’ve become so refined that today’s homes go up faster than ever. Some large developers, like those churning out entire neighborhoods, have crews that can put up a framed shell in just days.
Platform framing is the star. Basically, each floor forms a platform for the next, with walls stacked on top. This approach replaced older "balloon framing," which ran long, vertical members the full height of the house (a fire disaster waiting to happen, it turns out). Platform framing breaks up these vertical air channels, which slows the spread of fire slightly—a little trick that’s saved countless homes.
Beyond the bones, modern Type 5 construction mixes in engineered products. OSB sheathing replaces solid boards for walls and roofs; LVL beams hold up bigger spans without giant wood sizes. Instead of nailing everything by hand, builders use pneumatic nailers, framing squares, and special braces for seismic activity. In places like California and Florida, hurricane ties and hold-downs are standard to deal with earthquakes or high winds.
Exterior finishes? The options are endless. Vinyl siding, stucco, fiber cement, engineered wood—if you’ve wandered through Home Depot’s siding aisle, you know the drill. Brick veneer or stone sometimes get added too, but that’s just a thin facing, not the structural core.
Here’s a rundown of core elements in Type 5 construction:
- Dimensional lumber (2x4, 2x6, etc.) for wall studs and joists
- Plywood or OSB for roof and wall sheathing
- Engineered wood beams and trusses for wider spans
- Pre-fab metal connectors—hangers, hurricane ties, seismic braces
- Insulation tucked between framing (batts, spray foam, etc.)
- Water and air barriers (house wrap, vapor barriers)
- Gypsum drywall for interiors
The flexibility of Type 5 is a game-changer. You can stretch or shrink a floor plan, go one story or three, mix modern open concepts with old-school Craftsman charm—it’s all possible when everything is literally cut to fit.
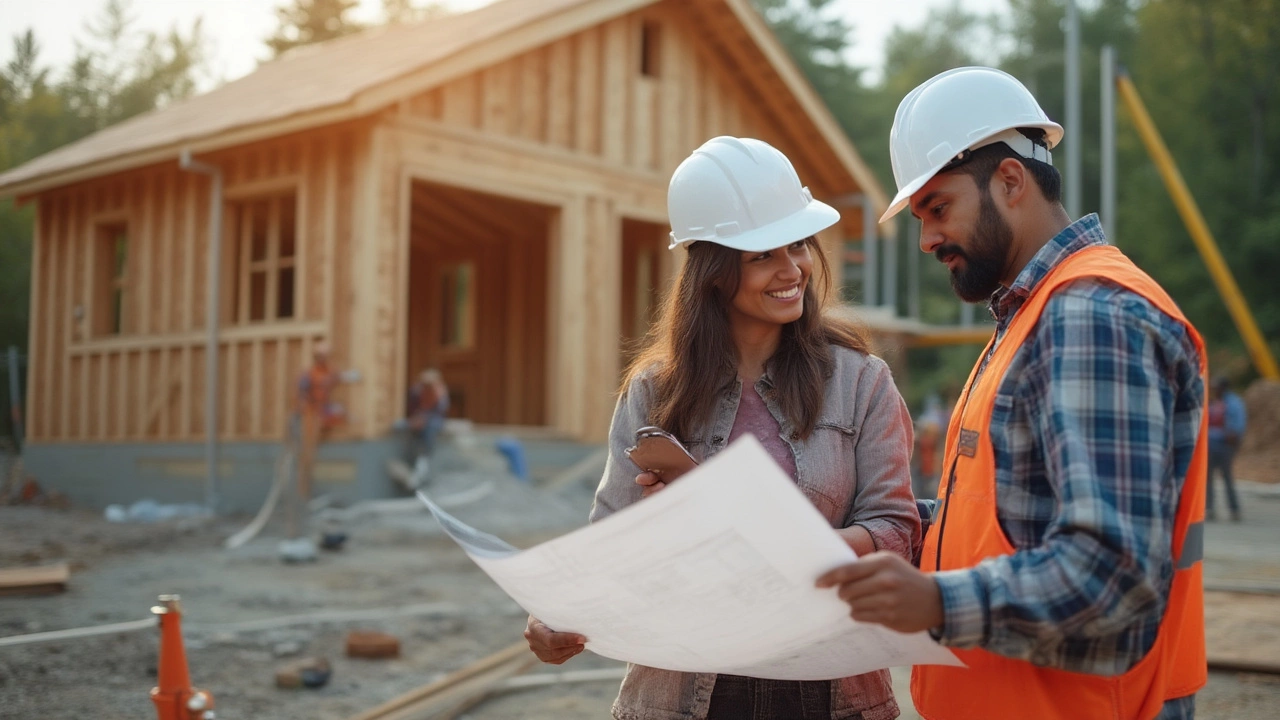
Risks, Codes, and Modern Safety Upgrades
Let’s talk straight—Type 5’s big weakness is fire. You put wood together, tough as it might seem, and there’s only so much you can do once flames get started. That’s why building codes layer on extra rules for Type 5 buildings.
Here’s a surprising stat: According to the National Fire Protection Association (NFPA), homes using light-frame wood construction can be consumed by fire in as little as 10 to 15 minutes after ignition, while concrete or masonry structures might last 60 minutes or more. With open framing, fire and smoke dash through the walls and attics at speeds most folks never expect. No wonder firefighters get nervous with a "working fire" in a wood-frame home.
But codes have gotten a lot tougher. After a rash of devastating suburban fires in the ’80s and ’90s, everything changed. Today, all Type 5 homes must use gypsum drywall on interior walls. That’s not just for a smooth finish—the drywall forms a 15-minute to 60-minute fire barrier, depending on thickness and layering. In multifamily buildings, extra-thick walls and floors separate units, toughening up escape chances and slowing the spread.
If you’ve ever pulled back insulation and stared at all the pink stuff, it’s not just there for warmth. Insulation also buys time during a fire, especially mineral wool or cellulose, which won’t contribute to burning as fast as foam.
Sprinklers, once rare in homes, have become standard in new apartments, condos, and even some townhomes. Check this out: A 2022 study from the Home Fire Sprinkler Coalition found that automatic residential sprinklers reduce chances of dying in a home fire by about 80%. Codes are pushing this hard, especially for multi-unit buildings.
Here’s a grab-bag of safety upgrades you’ll find in the best Type 5 new builds:
- 1/2" or 5/8" fire-rated drywall on walls and ceilings
- Fire-blocking material at floor-to-wall intersections and around pipes/wires
- Hardwired smoke and carbon monoxide detectors on every floor
- Fire-rated doors between garage and house
- Upgraded insulation in attics and party walls
- Automatic or manual fire sprinklers (often a code requirement for multifamily)
- Air-barrier wraps to keep smoke from spreading as fast
- Special roof designs (class A fire-rated shingles where wildfire risk is high)
New energy codes also mean Type 5 homes aren’t just safer, but more efficient. Wall assemblies get tighter, windows are double-glazed, and everything’s insulated like a thermos. In wildfire zones, builders now use metal mesh at attic vents and box in eaves with cement fiberboard—little details that stop embers from sneaking inside.
The table below lays out the basic fire performance for each construction type. See where Type 5 stacks up.
Construction Type | Main Structural Material | Fire Resistance | Typical Use |
---|---|---|---|
Type 1 | Reinforced concrete/steel | 2-3 hours+ | High-rises, hospitals |
Type 2 | Steel, non-combustible | 1-2 hours | Warehouses, schools |
Type 3 | Masonry exteriors, wood interiors | 1 hour+ | Urban condos, commercial |
Type 4 | Heavy timber | 1 hour+ | Mill buildings, historical |
Type 5 | Wood frame | Usually under 1 hour (w/o extra protection) | Homes, small apartments |
Knowing this, it’s clear that design, careful assembly, and smart upgrades keep Type 5 homes safer—and frankly, a lot more livable for families like mine and yours.
When to Choose Type 5 Construction: Pros, Cons, and Tips
So when does Type 5 make the most sense? If you want to build a single-family house, duplex, triplex, or even a small walk-up apartment, there’s a reason almost every builder leans towards this category. It’s cost-effective, flexible, and you can finish it almost anywhere without special equipment or a massive crew. The supply chain for wood and engineered products is huge, so delays—barring the wild swings of a pandemic—are usually manageable.
Modern Type 5 construction shines when you want indoor comfort on a budget. Families can enjoy open layouts, good soundproofing, and fast finishes. Remodeling or adding rooms later is also far easier than with heavy masonry. The simple nail-and-saw approach means almost every contractor or handyman knows the territory.
But here’s the flip side. Type 5’s reliance on wood comes with risks: fire, termites, water damage, and occasional mold. That’s why local knowledge matters. If you live in Florida, good luck skipping termite protection, and if you’re in the Rockies or California, you need to think about wildfire. Insurance rates sometimes sneak higher for wood frames compared to brick or concrete, especially in fire-prone parts of the country.
- Pro Tip: Ask your builder for records of fire-blocking details and insulation specs. Don’t just glance at pretty finishes—look for what’s behind the walls. Ask if the party walls (walls between units) reach all the way to the roof for fire stopping. It should.
- Get the attic, crawlspace, and basement checked every year for leaks or critters. Damage to wood framing isn’t always visible from the outside.
- If you’re remodeling, keep extra Type X drywall on hand. A little more doesn’t just soundproof a room; it buys escape time during a fire.
- Invest in smart smoke alarms—ones that network and send alerts to your phone. The faster you get a heads-up, the better your odds.
- Call your insurance agent and ask how fire-resistant upgrades will affect your premium. Some providers will knock a decent chunk off for sprinklers or class A roofing.
Plenty of homes have survived for a century or more using Type 5, as long as owners keep up with routine inspections and deal with water leaks ASAP. There’s a reason my own house—where Lyra and I raised Mabel—still feels solid after wild Texas thunderstorms and at least one wild barbecue incident gone wrong.
If you crave old-school craftsmanship, you can still get it with Type 5—think crown moldings, custom built-ins, and all the trimmings. It’s not about the materials so much as how they’re put together, finished, and protected for the long haul. That’s the real secret sauce to this most common, yet most misunderstood, building type.